
Environmental protection at Deutsche Giessdraht GmbH
Deutsche Giessdraht GmbH produces high-quality copper wire rod. Founded in 1975, the company is based in Emmerich am Rhein, with excellent connections to shipping and the road and rail networks. Aurubis AG has held 100% of the shares in Deutsche Giessdraht GmbH since 2018.
The 118 employees at DG produce up to 300,000 t of wire rod every year. The production process consists of melting, casting, rolling, pickling and winding the copper. The wire production facilities are state of the art and fulfill all product quality, environmental protection, and energy efficiency requirements.
The exhaust gas from the melting furnace is cleaned in a modern filter system, which ensures clear adherence to the limit values. The copper removal system integrated into production ensures that the wire cooling water is treated using state-of-the-art technology and that the monitoring values for copper in the cooling water fall well below the limit.
In recent years, we have invested in a number of projects to continuously modernize our plant. Today, an international comparison of wire rod plants has shown that Deutsche Giessdraht GmbH is very well positioned when it comes to energy efficiency. Introduced in 2012, the energy management system in accordance with ISO 50001 is a valuable aid in securing and further improving the level achieved. We consistently prevent waste and look for new recycling options to improve our waste balance further. This ensures that the company will continue to completely fulfill its ecological and economic responsibilities in the future as well.
The site has also successfully implemented an environmental management system in accordance with ISO 14001 and an energy management system in accordance with ISO 50001, which was successfully recertified in 2024.
Environmental protection Deutsche Giessdraht – facts & figures
Water is mainly used for cooling. Cooling water withdrawal is constantly adjusted to meet current consumption. The intelligent pump control system with variable rotational speed has sustainably reduced specific water consumption in recent years, although this is also subject to natural fluctuations.
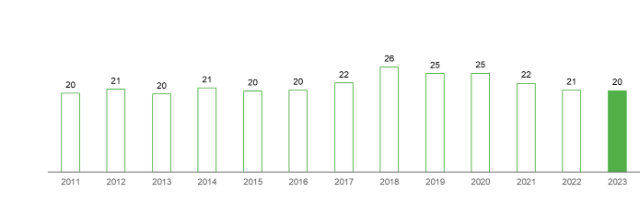
Water utilisation in m³/t of wire rod produced
Electricity is mainly consumed by the rolling mill, as well as by drives for pumps, compressors, blowers, lighting, etc. Thanks to the extensive modernization of components and the strict use of energy-efficient drive systems, it has been possible to reduce specific electricity consumption from 75 to 57 kWh/t of wire rod output since 2005 (a nearly 25 % reduction).
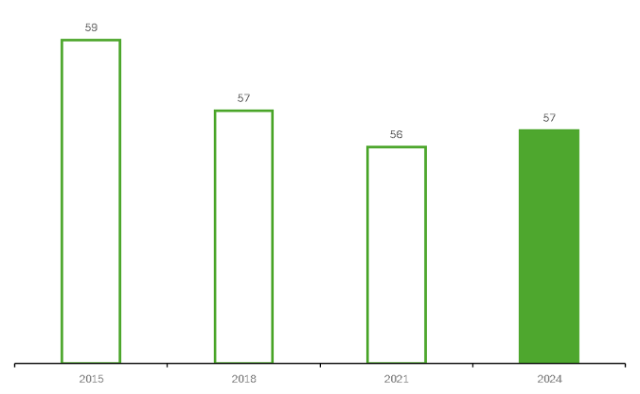
Specific energy consumption kWh/t wire rod
Environmental protection milestones
Water
- Receiving new discharge permit (until 2039)
Air
- Replacing all filter hoses in the exhaust gas purification system in July
Energy
- Replacing belt dryer (formerly gas) with infrared dryer
- Optimizing roller performance by installing frequency converter
- Replacing gas heater with infrared radiators
- Optimizing heating station operation (tundish)
Waste
- Obtaining new permit for the storage & use of high-purity copper scrap
- Optimizing the recycling rate
General
- Recertifying the environmental management system in June
- Receiving new permit to increase the doping material used
Current environmental goals and projects
- Decarbonization:
- Implementing the Group-wide decarbonization roadmap
- Status: in progress, concept submitted in October
Certificates
-
Um die heruntergeladene Komponente zu sehen den QR code scannen
DIN EN ISO 9001 : 2015 | 14001 : 2015 | 50001 : 2018 | 45001 : 2018
PDF
1 MB