
Our Process
Casting
-
The manufacturing process starts with a mixture of copper alloys and raw materials (copper, zinc, nickel, and others).
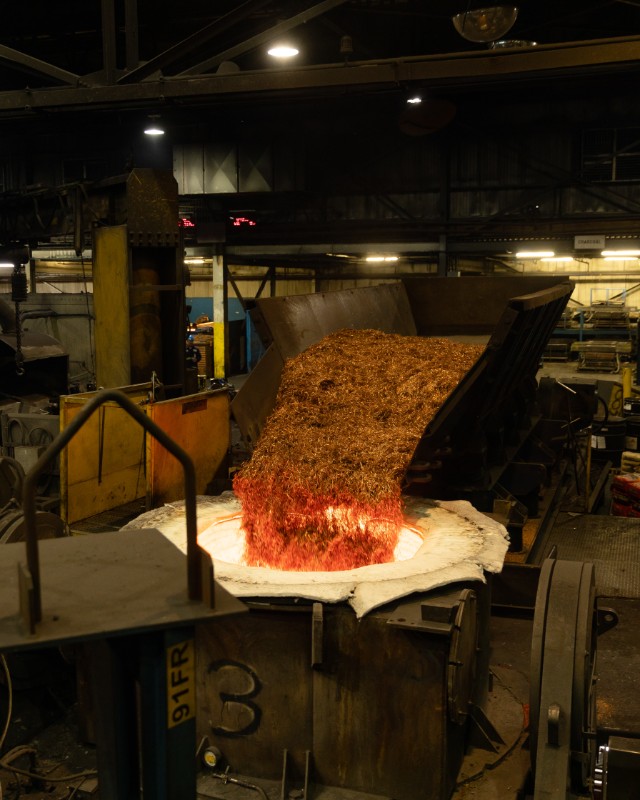
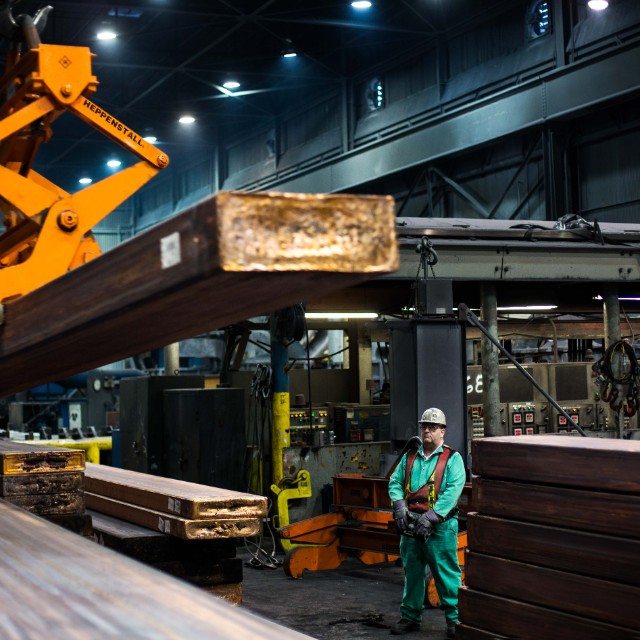
-
This metal is melted down in one of our casting furnaces and turned into large rectangular bars called "cakes."
-
After transportation by on-site rail, cakes are reheated and hot rolled into a coil form called "hot band."
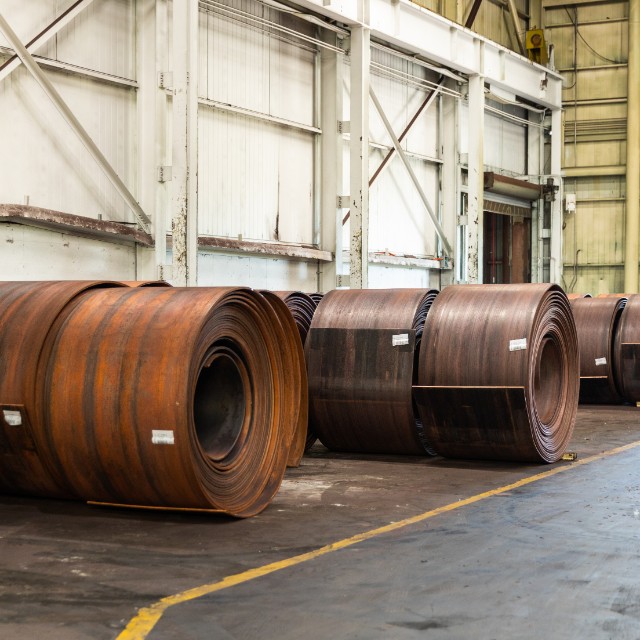
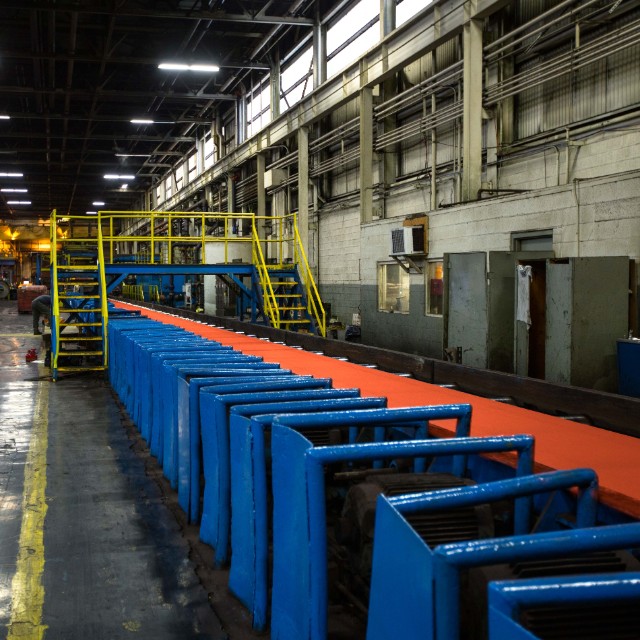
Reroll
-
After hot rolling, the surface edges are milled to remove surface impurities and oxidation.
⬇
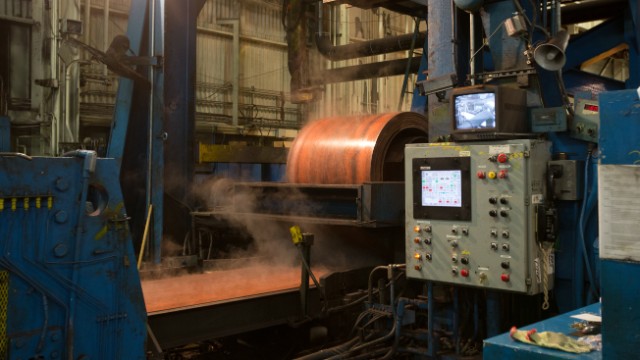
-
This is followed by breakdown rolling.
-
Thickness is dependent upon customer specifications.
-
⬇
Annealing
-
The thinner coil then follows a series of rolling and annealing steps. Hitting the customer's properties requires a very specific practice to be followed.
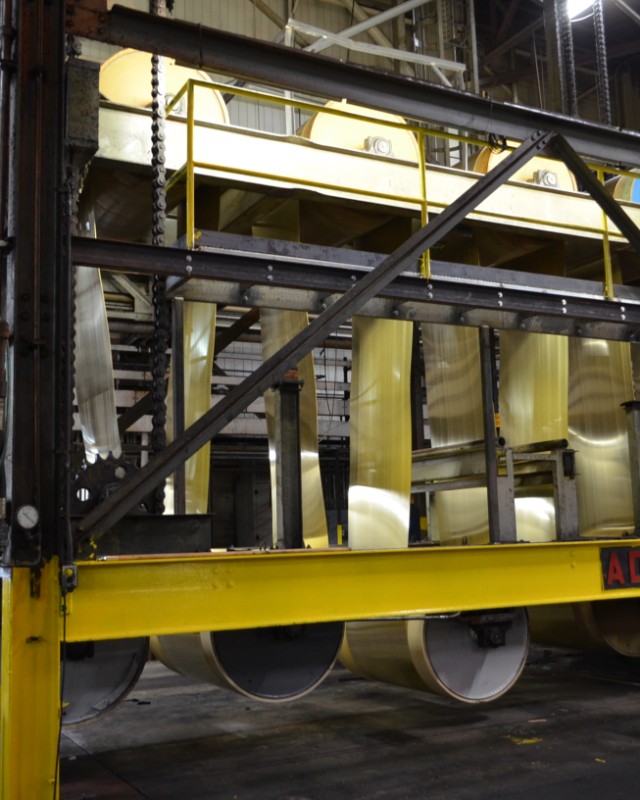
⬇
Finishing
-
Once final dimensions and properties are met, coils are sent to slitters to be cut to the customer specified width.
-
Coils are processed in our tension leveler or stretch bend leveler to create a flat surface.
-
In some cases, surface inspection may occur here.
-
-
A portion of the coils move on to our connector strip operations for tin coating or plating, then to traverse winding if required.
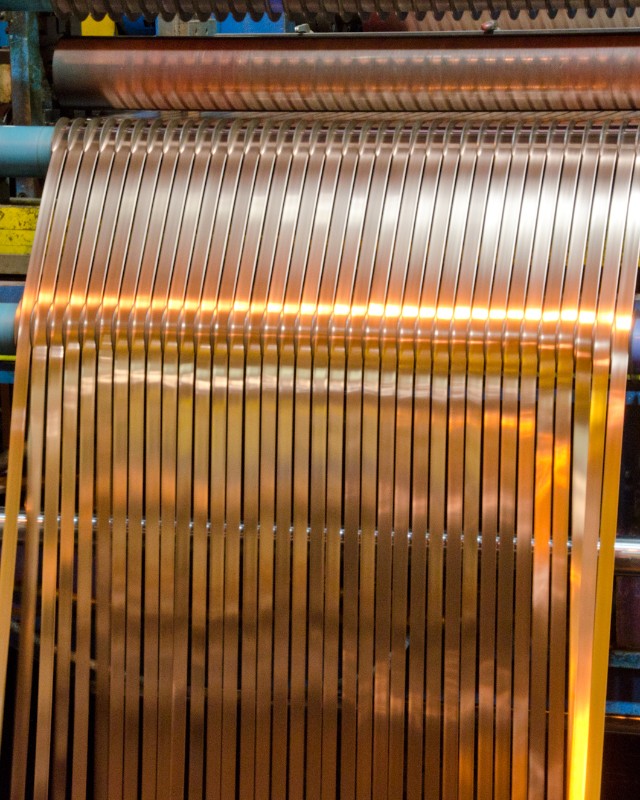
Packing & Shipping
-
At this point, materials are ready to be packaged for customer delivery!
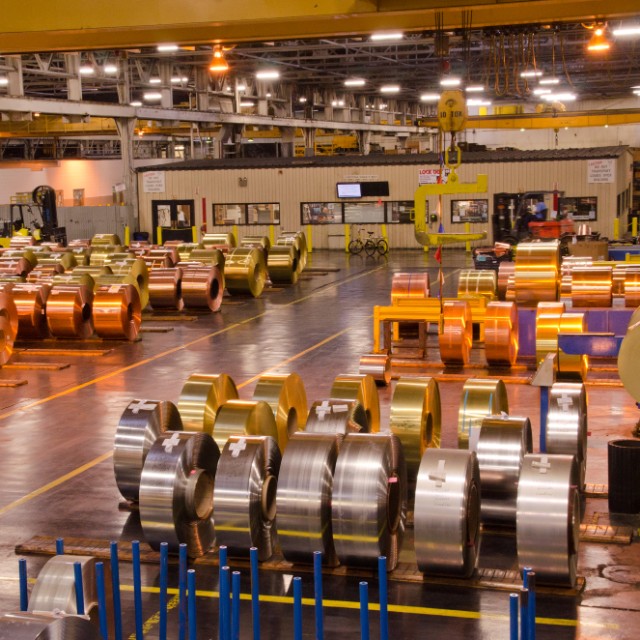
⬇
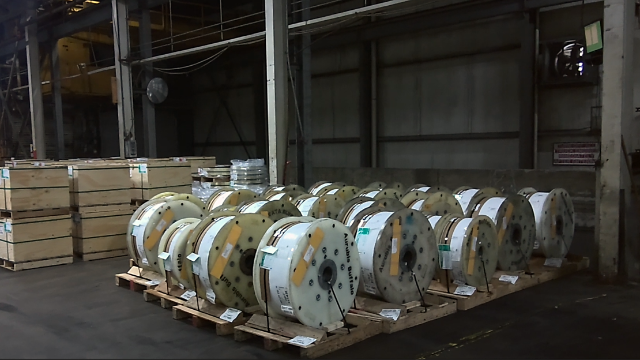